What Are New Coins Made Of
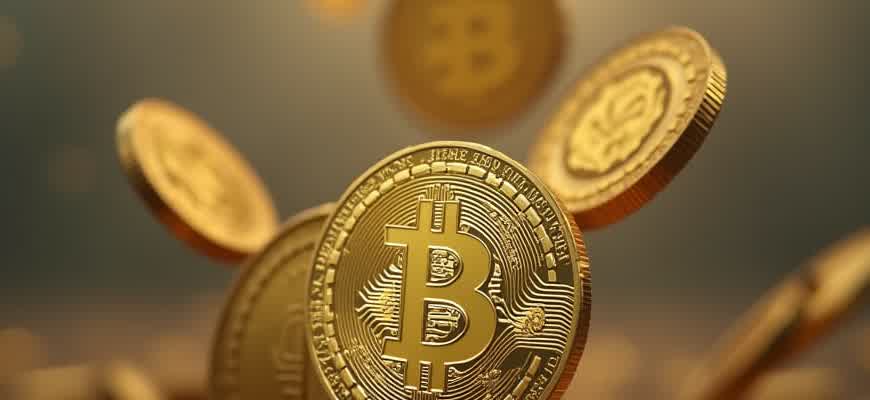
The composition of modern coins has evolved significantly over the years, influenced by factors such as cost, durability, and resistance to corrosion. New coins are made using various metals, often combining different elements to achieve the desired properties for circulation.
Below is a list of some of the most common materials used in minting modern coins:
- Steel – Often coated with nickel or copper for durability and corrosion resistance.
- Copper – A traditional material used for its excellent conductivity and ease of workability.
- Nickel – Provides resistance to corrosion and is often used in alloys to strengthen the coin.
- Aluminum – A lightweight, corrosion-resistant metal used in some low-value coins.
Alloy compositions are frequently tailored for specific coins. For example:
Coin | Material Composition |
---|---|
Penny | 97.5% Zinc, 2.5% Copper |
Nickel | 75% Copper, 25% Nickel |
Quarter | 91.67% Copper, 8.33% Nickel |
"The selection of materials not only affects the coin's physical properties but also its cost-efficiency and lifespan in circulation."
The Core Material of Modern Coins
Modern coins are manufactured using various metals to achieve durability, affordability, and distinct appearance. The choice of core material largely depends on the purpose of the coin, whether for everyday circulation or for commemorative purposes. These metals are usually combined with other materials to enhance their properties, such as corrosion resistance and ease of production.
The core material, often an alloy, is crucial in determining the coin's weight, feel, and overall longevity. Most coins today are made from a mixture of base metals, with some incorporating trace amounts of precious metals. The precise formulation of these alloys is a key factor in ensuring the coin can withstand the wear and tear of circulation.
Common Materials Used in Coin Cores
- Copper-Nickel Alloys - The most common combination for circulating coins, offering a good balance of durability and low cost.
- Steel Plated with Copper - A lightweight and cost-effective solution for smaller denomination coins.
- Bronze - Typically used for larger denominations or coins designed for commemorative purposes due to its aesthetic appeal.
- Cupronickel - A durable material, frequently used for high-value coins like silver dollars or similar currency.
Advantages of Alloyed Materials
"The choice of alloy affects not only the visual appearance of the coin but also its resistance to wear, corrosion, and overall longevity."
Alloys are preferred in coinage due to their ability to balance multiple requirements, such as strength, resistance to corrosion, and ease of minting. A well-chosen alloy can extend a coin’s lifespan and ensure that it maintains its quality during regular use over time.
Coin Composition Comparison
Material | Common Use | Properties |
---|---|---|
Copper-Nickel | Circulating Coins | Durable, corrosion-resistant, cost-effective |
Steel-Plated Copper | Small Denominations | Lightweight, inexpensive |
Bronze | Commemorative Coins | Visually appealing, resistant to corrosion |
Cupronickel | High-Value Coins | Strong, durable, attractive finish |
How Coin Composition Affects Durability and Wear
Coin composition plays a significant role in how long a coin lasts in circulation and how it withstands daily handling. Different materials and alloys have varying levels of resistance to physical wear, corrosion, and tarnishing. As coins are frequently exchanged and exposed to different environmental conditions, the choice of metals determines how quickly they degrade or maintain their appearance and functionality. In general, harder metals tend to resist scratching and denting, while more corrosion-resistant alloys prevent rust and degradation over time.
The physical characteristics of the materials used in coins also determine their longevity. For example, coins with a higher content of copper can be more prone to tarnishing, while nickel-based alloys may be more resilient. In recent years, many countries have moved toward using multi-layered or composite materials, which combine different metals to maximize both durability and cost-efficiency. These changes can significantly impact how quickly a coin shows signs of wear, such as fading details or losing its shape.
Factors Affecting Durability
- Hardness of the Metal: Coins made from harder metals resist scratches and deformations better.
- Corrosion Resistance: Some metals, like nickel and zinc, offer higher resistance to corrosion from moisture and chemicals.
- Alloy Composition: Coins that mix several metals can have balanced characteristics, such as strength and resistance to wear.
Common Coin Materials and Their Durability
Material | Durability | Resistance to Wear |
---|---|---|
Copper-Nickel | Moderate | Good |
Brass | Low | Moderate |
Steel-Copper Alloy | High | High |
Coins made of multi-layered alloys are designed to offer the best balance between longevity and cost-effectiveness, especially in countries with high circulation volumes.
Impact of Circulation on Coins
- Environmental Exposure: Coins exposed to humid conditions may develop surface corrosion over time.
- Handling: Frequent physical contact with other objects or coins can lead to wear, resulting in smoothness or loss of detail.
- Climatic Conditions: Extreme temperatures or direct sunlight can accelerate the oxidation process of certain metals.
The Role of Alloys in Coin Minting
Alloys play a crucial role in the coin minting process. The materials used in coin production significantly affect the durability, appearance, and cost-effectiveness of the final product. By combining different metals, mints can create materials that offer optimal properties for circulation and longevity. Different combinations of metals are employed depending on the type of coin being produced, its intended use, and the budget available for minting.
In coin production, the right alloy can improve resistance to wear, corrosion, and tarnishing. Alloys also allow for the customization of the coin’s color and weight, which can be important for distinguishing different denominations. By adjusting the proportions of metals in an alloy, mints can create coins that are both functional and aesthetically appealing.
Common Alloys Used in Coin Production
- Copper-Nickel – Often used in the production of lower-value coins, this alloy is known for its strength and resistance to corrosion.
- Cupronickel – A mix of copper and nickel, this alloy is widely used for coins that need to withstand wear while retaining their shine.
- Bronze – A mixture of copper and tin, bronze is used for higher-value coins and those intended for collectors.
- Silver – Historically used for high-value coins, silver alloys are still used for commemorative and limited-edition coins.
Properties of Common Alloys
Alloy | Durability | Corrosion Resistance | Cost |
---|---|---|---|
Copper-Nickel | High | Excellent | Moderate |
Cupronickel | Very High | Very Good | Moderate |
Bronze | Moderate | Good | Higher |
Silver | High | Excellent | High |
Alloys provide not only functionality but also a degree of aesthetic value, influencing the public’s perception of a coin's worth and longevity.
Why Alloys Matter in Minting
In addition to their practical advantages, alloys can also contribute to the security features of a coin. Some compositions are better at preventing counterfeiting, as specific alloys can be harder to replicate. This is why mints continuously experiment with and refine their alloy compositions, balancing factors such as durability, cost, and ease of recognition by the public.
Comparing the Materials Used in Different Countries
Coins around the world are produced from a variety of materials, often depending on the country’s economic status, cultural factors, and the intended use of the coins. Some countries use precious metals like gold or silver for their high-value coins, while others prefer durable alloys for everyday currency. The material choice influences the longevity, cost of production, and public perception of the currency. The differences in coin composition can also be seen as a reflection of national identity or economic priorities.
To better understand the differences, let’s examine how various countries approach the issue of coin material selection. Some nations prioritize cost-effective metals, while others use alloys that offer a balance between durability and aesthetic appeal. In many cases, these materials are a response to both economic conditions and the need to ensure the longevity of the coinage.
Common Materials Used Globally
- Copper – Often used in lower-value coins, copper provides durability and resistance to wear.
- Nickel – Typically combined with copper to create alloys, nickel enhances strength and corrosion resistance.
- Aluminum – Lightweight and inexpensive, aluminum is often used for coins of smaller denominations.
- Silver – A precious metal, silver is used in some countries for high-value coins and commemorative issues.
- Gold – Gold coins are generally used for investment purposes or as legal tender in high-value denominations.
Material Comparisons in Selected Countries
Country | Main Coin Materials | Common Uses |
---|---|---|
United States | Copper-nickel alloy | Low to mid-value coins (pennies, nickels, dimes, quarters) |
Eurozone | Copper, nickel, zinc alloys | Coins of various denominations (1 cent to 2 euros) |
Japan | Copper, zinc, nickel | Common circulation coins (1 yen, 5 yen, 10 yen, etc.) |
Switzerland | Cupronickel, nickel-brass | High-quality coins, including the 1 and 5 franc denominations |
Many countries, such as the United States and Japan, use copper-nickel alloys for most of their circulating coins. These alloys are chosen for their strength, cost-effectiveness, and resistance to corrosion.
- Economic Efficiency: Some nations opt for cheaper materials like aluminum or steel to keep production costs low.
- Durability: Higher-value coins, such as those made from silver or gold, are often used for investments rather than day-to-day transactions.
- Cultural Significance: In some countries, specific metals are chosen for their cultural or symbolic importance.
The Environmental Impact of Coin Production Materials
The materials used in the production of coins can have significant environmental consequences. These impacts stem not only from the extraction of raw materials but also from the energy-intensive processes involved in minting. Coins are traditionally made from metals such as copper, nickel, and zinc, but as new coins are introduced, alternative materials are also being explored. Each of these metals has a different ecological footprint that affects air, water, and soil quality.
Additionally, the disposal and recycling of coins play a role in their environmental cost. While some metals are recyclable, the logistics and energy required to collect and process them can still be quite taxing on natural resources. In this context, governments are beginning to explore the use of more sustainable materials, which could potentially reduce both the carbon footprint and long-term environmental harm associated with coin production.
Key Materials Used in Coin Production
- Copper: Widely used in coins due to its durability and ease of minting. However, copper mining has significant environmental impacts, including habitat destruction and water contamination.
- Nickel: Often alloyed with copper to make coins more resistant to wear. Nickel extraction can release harmful substances into nearby ecosystems, and its mining process is energy-intensive.
- Zinc: A less toxic option, but its extraction and processing contribute to significant carbon emissions.
- Polymer-based materials: A growing alternative to metal coins in some regions, but their production involves plastics, which are not always easily recyclable.
Environmental Concerns in Coin Manufacturing
- Extraction of Raw Materials: Mining activities lead to land degradation, habitat loss, and pollution. The process consumes large amounts of water and energy.
- Energy Consumption: The manufacturing process of coins requires high temperatures for melting metals, which results in significant carbon emissions.
- Disposal and Recycling: Coins can be recycled, but collection and sorting require substantial energy. Not all regions have efficient recycling systems, leading to unnecessary waste.
"The extraction and processing of metals for coin production can contribute significantly to environmental pollution, and even post-production recycling may not fully offset the ecological damage." – Environmental Analyst
Comparison of Environmental Impact by Material
Material | Environmental Impact |
---|---|
Copper | High due to mining and energy use in production. |
Nickel | Moderate to high; significant pollution during extraction. |
Zinc | Moderate, with a relatively low environmental footprint compared to copper and nickel. |
Polymer | Potentially lower if recycled, but plastic production remains a concern. |
Innovations in Coin Materials: What’s Next?
The continuous evolution of currency design and production has led to new materials being explored for coinage. Traditional metals like copper and nickel have long been the staples of minting, but technological advancements and sustainability concerns have driven the search for alternatives. These innovations not only aim to improve the durability and functionality of coins but also consider environmental impacts and cost-effectiveness. As the world moves towards more sustainable solutions, new materials might soon replace the metals that have dominated coinage for centuries.
One key driver of this shift is the growing demand for eco-friendly production processes. As governments and mints explore more sustainable options, we’re seeing increased use of composite materials, bioplastics, and even recycled metals. In addition to environmental benefits, these new materials may also offer enhanced resistance to wear and corrosion, extending the life of coins. But what exactly can we expect in the near future when it comes to materials used in coin production?
Promising Materials for the Future
- Recycled Metals: Increasing focus on reducing waste has led to the recycling of metals from old coins and scrap. This not only conserves resources but also reduces energy consumption during production.
- Bioplastics: Some mints are experimenting with plant-based polymers, which can be used for low-value coins, reducing the environmental footprint and reliance on traditional metals.
- Advanced Alloys: Alloys made from a combination of materials like aluminum, zinc, and magnesium offer high durability and resistance to corrosion, while being lighter and cost-effective.
Key Factors Driving Change
- Environmental Impact: The need for sustainable materials is pushing the development of alternatives that have less negative impact on the planet.
- Cost Efficiency: New materials often provide cheaper manufacturing costs and increased longevity, benefiting both mints and the general public.
- Technological Advancements: Advances in metallurgy and material science are opening doors to more innovative and practical options for coin production.
Material Comparison
Material | Benefits | Challenges |
---|---|---|
Recycled Metals | Reduced waste, lower energy consumption | Limited availability, may not meet all durability requirements |
Bioplastics | Environmentally friendly, reduces reliance on metals | Durability concerns, higher initial costs |
Advanced Alloys | Lightweight, cost-effective, durable | Potential for higher production costs due to complex processes |
"As the world turns its attention to sustainability, coin materials are evolving to meet new environmental and economic standards. Innovations like bioplastics and advanced alloys represent just the beginning of this shift."
How Changing Coin Materials Affect Collectors and Value
When new materials are introduced in coin production, it can significantly impact the coin’s appeal among collectors. The material choice often influences the coin's aesthetic qualities, durability, and overall market value. These shifts in composition can either increase or decrease interest in certain coins, depending on how they affect these factors. For example, when a coin's metal content changes, it may lose or gain historical value, which is crucial for many collectors.
Collectors often place high value on the rarity and uniqueness of a coin, both of which can be influenced by the materials used. When the composition is altered to include more common or less durable materials, it can reduce the long-term desirability of the coin. On the other hand, using rare or precious materials can elevate its status in the market and among enthusiasts.
Impact on Market Trends
Changes in the materials used for coinage can cause notable shifts in market trends. For example:
- Material Substitution: Shifting from silver to copper or nickel often reduces the intrinsic value of a coin.
- Increased Durability: Coins made from more durable metals may have a longer lifespan, which can make them more appealing for long-term collection.
- Unique Alloys: Special edition coins with rare alloys can boost collector interest and value.
Collectors' Response to Material Changes
Collectors’ reactions to changes in coin materials can vary depending on their investment priorities and the perceived value of the new composition.
- Historical Context: Some collectors may focus on coins made from metals that are historically significant.
- Rarity and Demand: A shift to rarer materials can create high demand, which drives up the price.
- Authenticity Concerns: Using materials that are not traditional may lead some collectors to question the authenticity of the coins.
Key Points to Consider
"Material choices for coins have always played a pivotal role in determining their desirability among collectors. Changes in composition can lead to higher or lower demand, impacting their long-term value."
Comparison of Different Coin Materials
Material | Durability | Collector Value |
---|---|---|
Silver | High | High |
Copper | Moderate | Moderate |
Nickel | High | Low to Moderate |
Gold | Very High | Very High |
The Economic Drivers Behind Changes in Coin Materials
The cost-effectiveness of coin production plays a pivotal role in determining the choice of materials used for minting new coins. As metal prices fluctuate, governments are compelled to reassess their coinage compositions to ensure that production remains affordable. The decision to shift from traditional materials like copper and nickel to less expensive alternatives is often a response to the rising cost of raw materials and the growing economic pressures on national treasuries.
Additionally, innovations in materials technology, such as the use of polymers or alloys that simulate the appearance of precious metals, have also influenced the shift in coin compositions. These advances not only help reduce costs but also contribute to the durability and security of coins, which is crucial for maintaining public trust in a currency system.
Key Economic Factors Driving Material Shifts
- Production Costs: The rising prices of raw metals like copper, zinc, and nickel have made traditional coinage more expensive to produce.
- Durability Considerations: Coins made from more resilient materials can last longer, reducing the need for frequent replacements.
- Supply Chain Stability: Some materials may be sourced from regions with unstable supply chains, prompting a shift to more locally available resources.
Common Alternatives to Traditional Metals
- Steel Alloys: Steel-coated with a thin layer of copper or nickel is increasingly being used for low-value coins.
- Polymer-based Coins: Some countries are experimenting with polymer-based coins, which are lightweight and cost-effective.
- Aluminum Alloys: Aluminum is being used for coins in some regions due to its low cost and resistance to corrosion.
"Shifting coin materials is not only a cost-saving measure but also a response to technological advancements that improve the longevity and usability of currency."
Comparative Cost Breakdown of Different Coin Materials
Material | Production Cost per Coin | Durability |
---|---|---|
Nickel-Copper Alloy | $0.12 | High |
Steel with Copper Coating | $0.05 | Medium |
Polymer Composite | $0.03 | High |